High Precision Plastic Injection Molding: Revolutionizing Manufacturing
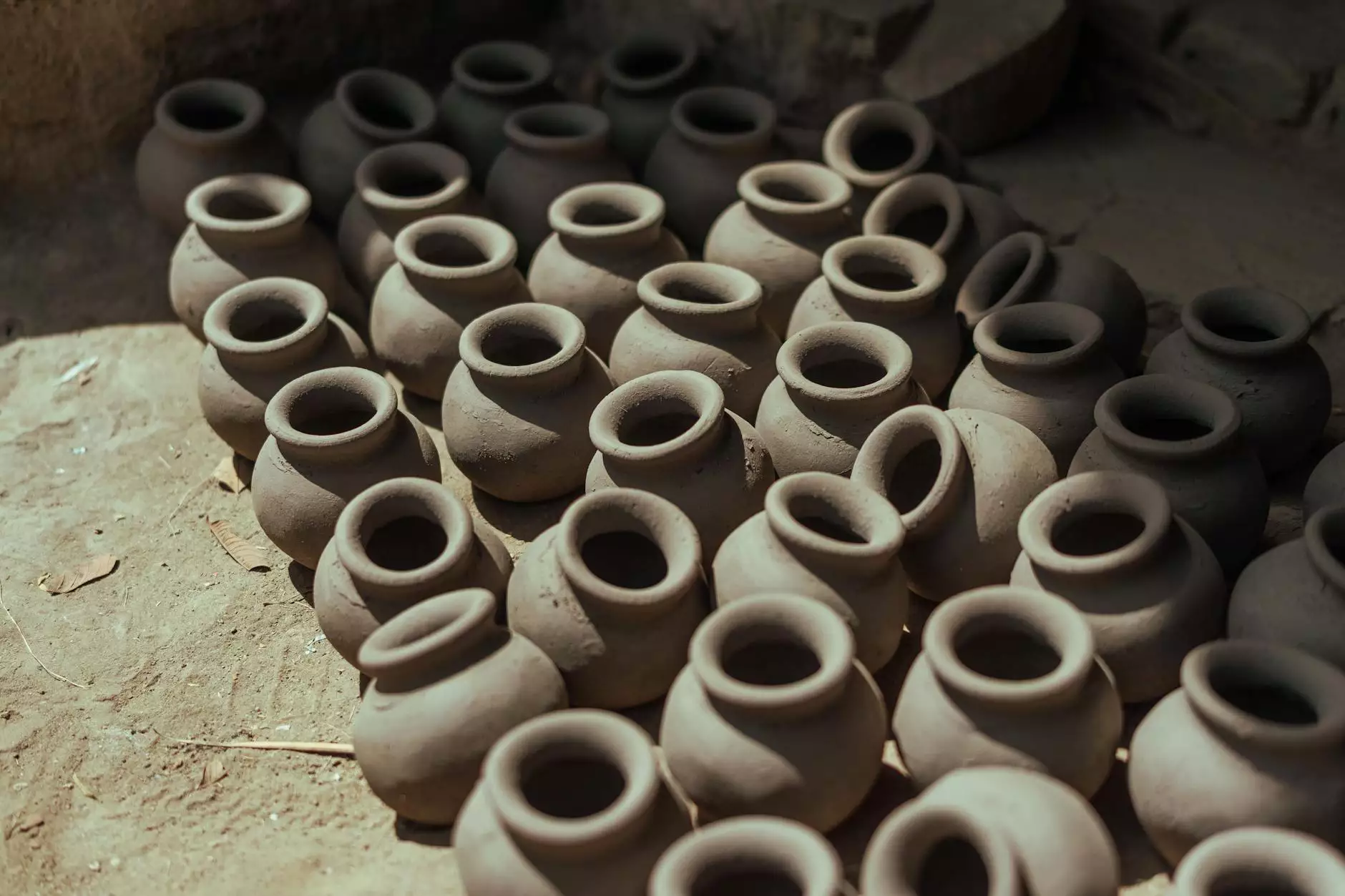
High precision plastic injection molding is not just a manufacturing process; it is a critical technology that has transformed various industries through its ability to produce complex parts with exceptional accuracy and efficiency. As the demand for precision components continues to surge in sectors such as automotive, medical, consumer goods, and electronics, understanding the intricacies of this process becomes vital for businesses looking to maintain a competitive edge.
Understanding High Precision Plastic Injection Molding
At its core, plastic injection molding is a method where molten plastic is injected into a mold to create parts of varying shapes and sizes. The term high precision refers to the tight tolerances and exact specifications that manufacturers can achieve. This process allows for intricate designs, repeatable quality, and scalability, making it a preferred choice for mass production.
How It Works
The process of high precision plastic injection molding can be broken down into several key stages:
- Material Preparation: The first step involves selecting the appropriate thermoplastic material which is then dried to remove moisture.
- Injection: The dried plastic is fed into an injection machine where it is heated until it becomes molten.
- Molding: The molten plastic is then injected into a precisely engineered mold under high pressure.
- Cooling: After filling the mold, the plastic is allowed to cool and solidify, taking the shape of the mold cavity.
- Ejection: Once cooled, the newly formed part is ejected from the mold, ready for finishing or assembly.
Benefits of High Precision Plastic Injection Molding
Choosing high precision plastic injection molding comes with numerous advantages:
- Consistency and Reproducibility: One of the hallmarks of this process is its ability to produce large quantities of identical parts with minimal variance.
- Cost-Effectiveness: While the initial setup might be costly, the efficiency and speed of production significantly reduce per-unit costs, particularly for large runs.
- Design Flexibility: Advanced design capabilities allow for complex geometries that are often impossible to achieve with other manufacturing methods.
- Material Variety: A wide range of plastic materials can be used, each offering unique properties suitable for different applications.
- Reduced Waste: The precise nature of the process minimizes material waste, which is not only cost-effective but also environmentally friendly.
Applications in Various Industries
The versatility of high precision plastic injection molding enables it to be utilized across various sectors:
Automotive Industry
In the automotive sector, this technology is widely used to create lightweight, strong components such as dashboard panels, exterior trims, and intricate assemblies that enhance vehicle functionality and aesthetics.
Medical Devices
For medical applications, precision is crucial. Injection-molded parts such as syringes, surgical instruments, and housings for diagnostic devices require stringent adherence to safety and regulatory requirements, which is adeptly supported by this manufacturing method.
Consumer Electronics
The consumer electronics industry benefits from high precision molding in producing lightweight casings, connectors, and other components that require a tight fit and precise performance.
Consumer Goods
From toys to kitchenware, the ability to mold complex shapes quickly and cost-effectively makes high precision plastic injection molding a go-to solution for many consumer goods manufacturers.
Best Practices in High Precision Plastic Injection Molding
To harness the full potential of high precision plastic injection molding, manufacturers should adopt best practices:
1. Material Selection
Choosing the right material is paramount. Factors such as strength, flexibility, temperature resistance, and chemical compatibility should guide the decision.
2. Mold Design
A well-designed mold reduces defects and ensures high precision. Integrating cooling channels and ensuring optimal shrinkage rates can enhance the process significantly.
3. Process Optimization
Continuous monitoring of the injection parameters—temperature, pressure, and speed—can lead to improvements in product quality and consistency.
4. Quality Control
Implementing rigorous quality control procedures at every stage can help catch defects early. Utilizing advanced inspection technologies can significantly reduce production errors.
Challenges in High Precision Plastic Injection Molding
While the advantages are compelling, there are challenges that manufacturers must navigate:
1. High Initial Costs
The cost of mold design and manufacturing can be substantial, making it crucial for businesses to conduct thorough cost analyses before proceeding with production.
2. Long Lead Times for Molds
Creating high-quality molds can take time. Businesses need to plan adequately to avoid delays in production schedules.
3. Complex Process
The technical expertise required for setting up and optimizing the injection molding process can be a barrier for some companies. Continuous training and investment in skilled labor are essential.
The Future of High Precision Plastic Injection Molding
The landscape of high precision plastic injection molding is rapidly evolving. Emerging technologies such as 3D printing, automation, and Industry 4.0 advancements are influencing the future of the industry. Here’s how:
1. Integration with 3D Printing
3D printing technology is being utilized to create prototypes and custom molds, streamlining the development process and reducing time to market.
2. Automation and Robotics
The integration of robotics in injection molding processes enhances precision and efficiency, allowing for faster production cycles and reducing the risk of human error.
3. Industry 4.0
With the rise of the Internet of Things (IoT), manufacturers can leverage data analytics for predictive maintenance, ultimately improving uptime and reducing costs.
Conclusion
In summary, high precision plastic injection molding is a transformative technology that is pivotal for modern manufacturing. Its ability to produce high-quality, consistent products has made it an invaluable asset across various industries. As the manufacturing landscape continues to change, staying informed about advancements and best practices will be essential for businesses to thrive in this competitive environment.
For more information on how high precision plastic injection molding can benefit your business, visit deepmould.net, where innovation meets precision in manufacturing.